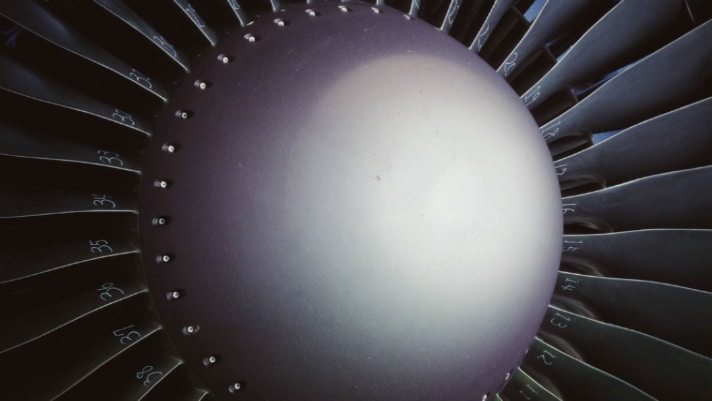
Compressed air distribution systems are used in homes, auto body shops, construction sites, and more. Because they have such a large range of applications, the systems must work efficiently; otherwise, it could lead to significant financial losses.
One of the biggest challenges with air compressor piping is pressure drop. A pressure drop describes the difference between the point discharge and the point of use within the system. Typically, the difference in pressure should be no more than 10%.
If an automotive air compressor distribution system has a greater difference than 10%, it will lead to losses and high energy bills. This article examines some of the factors that may cause pressure to drop within an air compressor piping system.
Air Quality Challenges
One of the factors that can cause a significant pressure drop in a system is air quality. Air used in commercial applications, such as in an automotive air compressor, is graded according to its purity. Too many impurities within the system will cause resistance to airflow.
There are three main contaminants that can cause a pressure drop within the system:
Water Vapor: Water vapor is almost always present in the air and is often introduced at the point of intake. Water can cause damage to internal components, especially when mixed with corrosive gases. Care should be taken not to introduce water at the entry point. Vapor content within an automotive air compressor can be measured using the pressure dew point temperature.
Oil: Oil within the air compressor piping can be problematic and can increase the overall load of the system.
Gases and Fumes: Gases and fumes are airborne and can carry corrosive compounds that can damage internal components. Furthermore, these gases can be problematic at the point of use. For certain applications such as in medicine and indoor use, the quality of the output air must be high.
Distribution and Supply in Air Compressor Pipes
The supply and distribution within the air compressor pipes should be consistent and uniform. If the consistency of supply is compromised in your automotive air compressor, it will result in poor tool performance, high energy bills, and low-productivity. Steps should, therefore, be taken to prevent leakages and pressure drops within the air compressor.
Pressure drops are often only identified in the main pipes. But care should be taken to ensure that other pipes within the distribution system adhere to the pressure level standards. Also, when trying to determine the drop, all points must be factored into the calculation. Some of the components in the system that may compromise distribution include poorly sized tubing, piping tees, lubricators, and leaking hoses.
Hoses, fittings, and connectors, should have a difference not exceeding 0.1 bar between the intake and the discharge point.
To address the problem, some technicians may opt to increase the pressure to compensate for the drop. Unfortunately, by increasing the working pressure, the demand at the point of use increases. The result is an output pressure that is higher than required. So, trying to correct the pressure difference by increasing the input is not recommended as a final solution when addressing the issue.
The dimensions, the design, and the routing of the compressed air tubing must be effective to ensure good performance and productivity. The system should be designed such that it keeps the pressure drop to a minimum.
How to Minimize the Pressure Drop
When installing an air compressor system, it is important to pay attention to the layout and the design. Taking time to understand the requirements for the layout will reduce errors when installing an automotive air compressor.
The compressor should ideally be placed in a convenient location to reduce the length of the piping. Where the compressor is placed will also be determined by the quality of air and availability of space to facilitate airflow. Some designers may use piping with loops to contain moisture. All in all, the design stage is critical in reducing the risk of a pressure drop and should not be ignored.
For more information about air compressor pressure drops and maintenance, contact Rapid Air Products today.